
Hinter den Kulissen:
So funktioniert ein Sägewerk
Wo gehobelt wird, da fallen bekanntlich Späne. Und an kaum einem Ort gibt es so viele davon wie in einem Sägewerk – doch wie funktionieren diese Hightech-Anlagen überhaupt? Wie viel Holz wird dort täglich verarbeitet und was sind die wichtigsten Schritte dabei? Wir werfen einen Blick hinter die Kulissen.
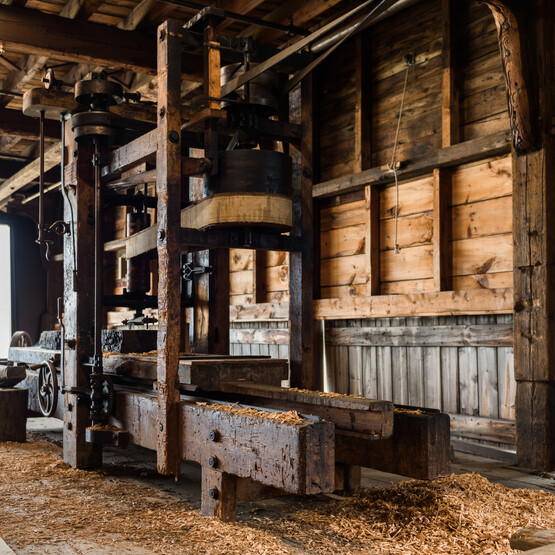
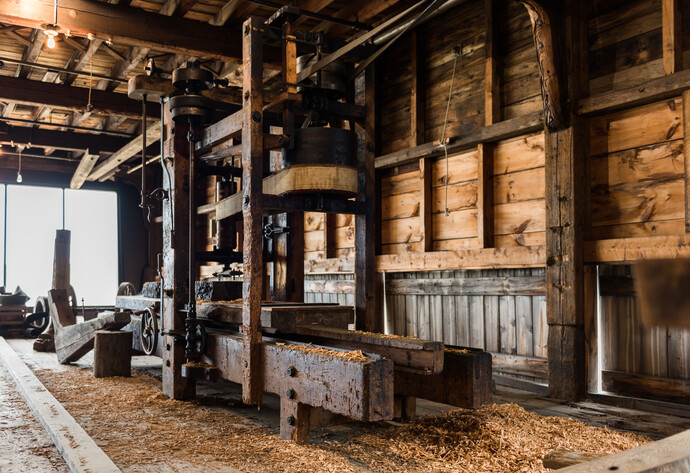
Moderne Sägewerke: schneller und effizienter
Ob für den Bau von Möbeln, von Wänden für Fertighäuser oder für die Nutzung als Parkett- oder Dielenböden: Nach dem Fällen eines Baumes sind zahlreiche Schritte nötig, um das Holz zu verarbeiten und nutzbar zu machen. Früher war dieser Prozess langwierig und kompliziert. Bevor die Maschinen automatisiert und Prozesse aufeinander abgestimmt wurden, war Handarbeit gefragt. Was früher mehrere Tage gedauert hat, ist heute in Sekundenschnelle erledigt. Mechanische Anlagen für den Holzschnitt, bei dem der Rahmen erst angehoben und dann gesenkt wird, um durch die Schwerkraft das Sägeblatt am Stamm entlanglaufen zu lassen, gibt es heute fast nur noch in Museen. Sägen wurden nicht elektrisch, sondern häufig mithilfe von Wasserkraft angetrieben.
Ein modernes Sägewerk funktioniert da gänzlich anders. Übrigens: Die mit Abstand meisten Holz verarbeitenden Betriebe Deutschlands gibt es in Bayern (219), Nordrhein-Westfalen (215) und Baden-Württemberg (209).
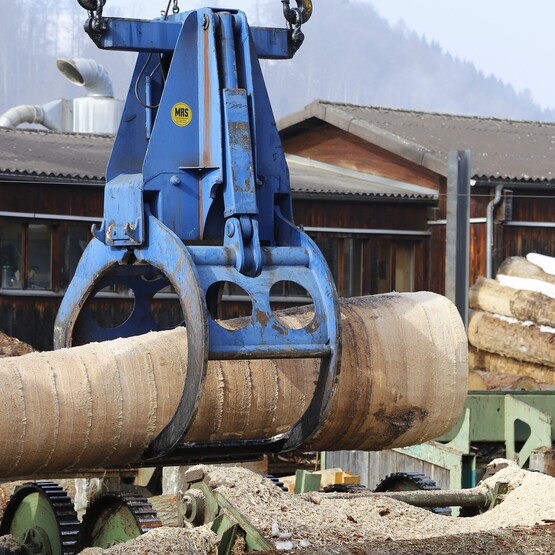
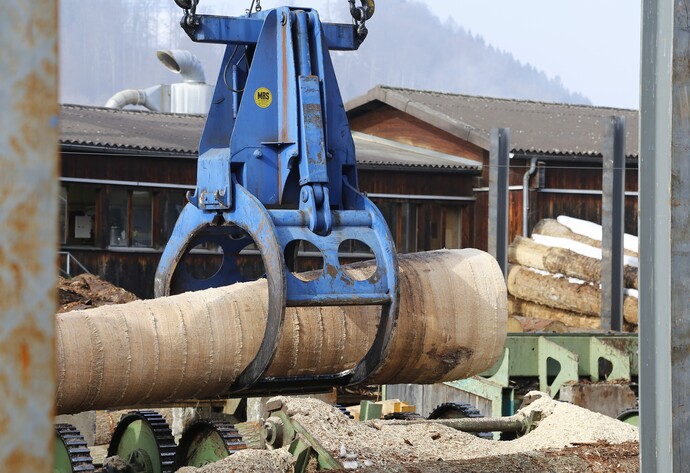
Hier fängt alles an: der Rundholzplatz
Alles beginnt auf dem Rundholzplatz. Nach der „Ernte“ werden die grob entasteten Rundstämme in einer speziellen Anlage – ähnlich einer riesigen Drechselmaschine – entrindet und dann auf dem Rundholzplatz abgeladen. Während dieses Arbeitsschritts werden die Stämme zudem vermessen und sortiert. Dabei geht es vor allem um die Frage, wie gerade der Stamm ist und welche Balken-Typen sich daraus gewinnen lassen. Ist ein Stamm sehr schief, eignet er sich eher für kürzere Holz-Elemente. Je nach Größe der Bäume können die Rundhölzer deutlich über zehn Meter lang sein. Mit speziellen Rundholzbaggern und -kränen sowie am Boden verlaufenden Förderbändern werden sie hier sortiert, gestapelt und später weitertransportiert.
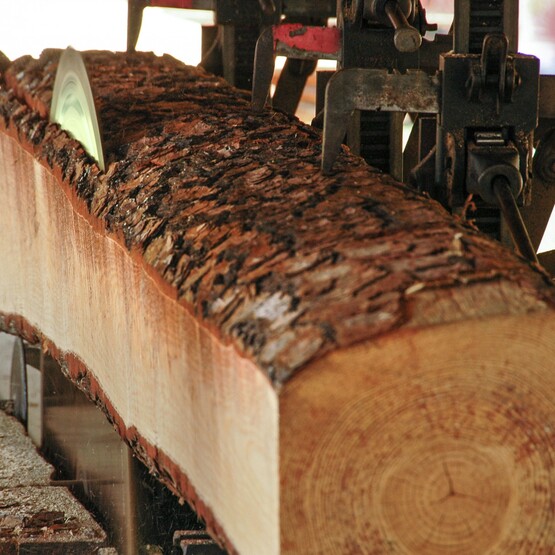
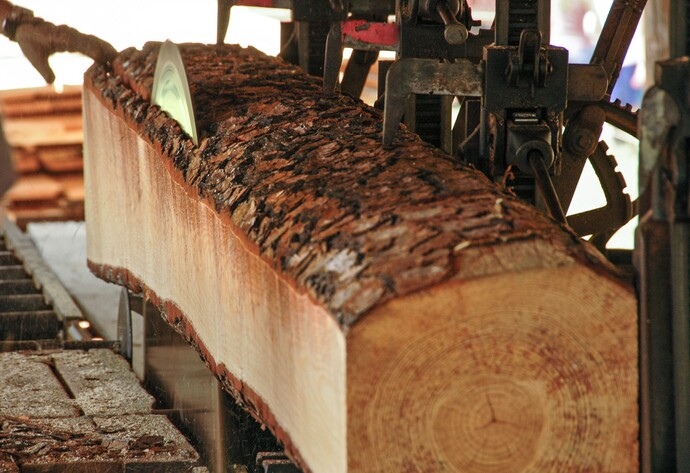
Hier wird Rundes eckig: Zerspanung und Einschnittlinie
Danach gelangen die Rundhölzer in die Ablängstation. Der Name ist Programm: Hier werden sie auf zuvor definierte Längen gebracht, um bestmöglich weiterverarbeitet werden zu können. Haben sie die richtige Länge, geht es ins Herz eines jeden Sägewerks.
In der anschließenden Einschnittlinie geht es richtig rund – oder besser gesagt: eckig. Mit industriellen Sägen wie riesigen Band- und Gattersägen werden die Rundhölzer hier in breite Streifen geschnitten, aus denen später Balken, Bretter und Kanthölzer entstehen. Die Zerspaneranlage ist eine besondere Form der Einschnittlinie, hier wird mit modernen Kreissägen gearbeitet. Bevor es jedoch ans Schneiden geht, wird in modernen Sägewerken ein Schnittplan für jeden Stamm erstellt, um so wenig Ausschuss wie möglich zu produzieren. Aus dem abgefrästen Äußeren der Stämme werden beispielsweise Hackschnitzel hergestellt, auch das beim Schneiden entstehende Sägemehl wird weiterverwendet – Abfall gibt es in einem Sägewerk kaum.
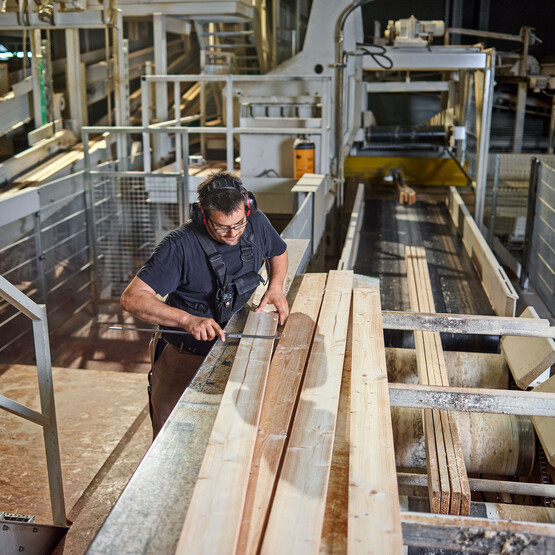
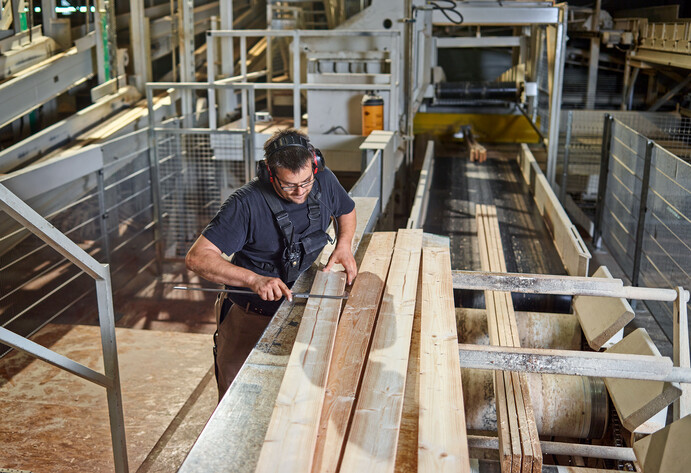
In neue Form gebracht: hobeln & biegen
Nicht alle Bretter bleiben auch Bretter. Einige von ihnen werden im Hobelwerk weiterverarbeitet und dort durch das Abholen ihrer Oberfläche in eine neue Form gebracht. Hier werden sie zu sogenannten Profilhölzern mit einer glatten Oberfläche verarbeitet, die beispielsweise im Saunabau und bei Holzdecken oder -böden Anwendung finden. Für andere Bereiche braucht es aber auch Holz mit einer bestimmten Krümmung – das wird in der Biegestation hergestellt. Unter vorsichtigem Druck werden die Hölzer erst verleimt und bevor der Leim trocken ist in die Biegemaschine eingespannt, um dort in Form gebracht zu werden. Bis alles ausgehärtet ist und das Holz seine Biegung beibehält, kann es mehr als einen halben Tag dauern.
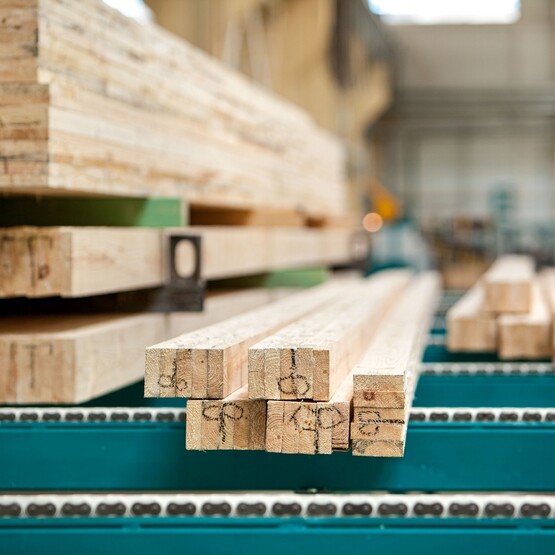
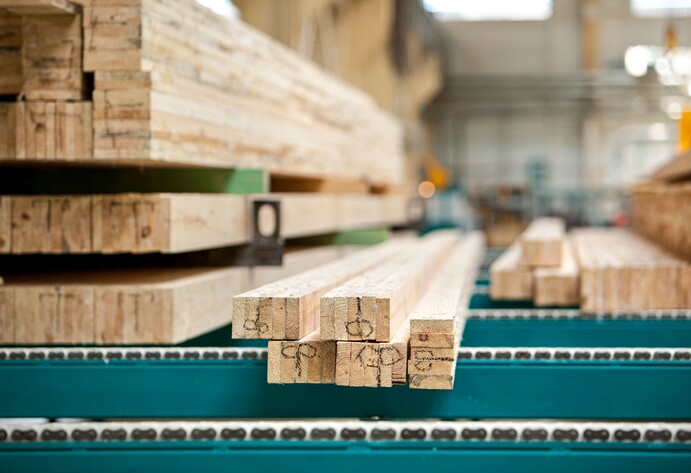
Hier kommt es auf jeden Millimeter an: das Sortieren
Was früher Menschen mit dem Auge und den Händen übernahmen, machen heute präzise Laser: Die Bretter und Hölzer werden exakt vermessen und geprüft. Nicht nur auf ihre Stärke, Breite und Länge, sondern ebenfalls auf den geraden Verlauf ihrer Kanten und eventuelle fehlerhafte Stellen im Holz. Anschließend sortieren Roboter die Bretter und Balken je nach Größe und Stärke
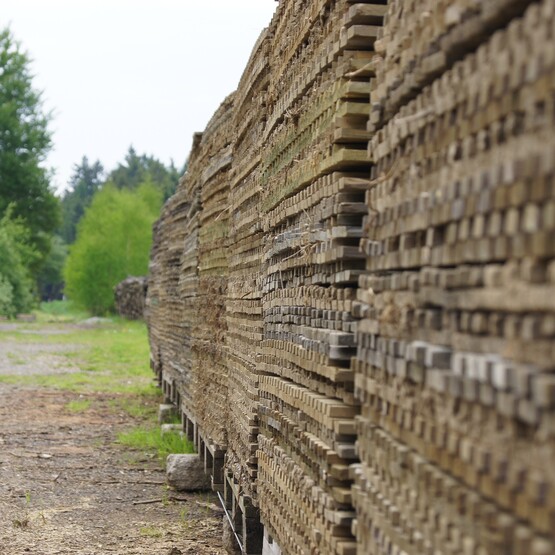
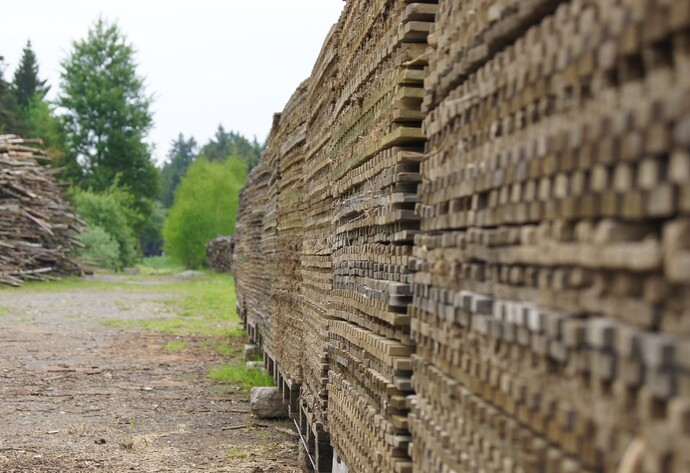
Gut Holz will Weile haben: die Ablagerung
Damit das Holz später nicht mehr so viel arbeitet und sich verändert, wird es bei der Ablagerung so gestapelt, dass von allen Seiten Luft an die Bretter und Hölzer gelangen kann. Für die meisten Anwendungsfälle – vom Brennholz bis zum Möbel- oder Hausbau – empfiehlt sich eine Feuchtigkeit von knapp unter 20 Prozent. Bei Brennholz sollten es im Optimalfall zwischen 16 und 18 Prozent sein – hat es weniger, verbrennt es zu schnell. Bei zu viel Feuchtigkeit kommt es zu stärkerer Rauchbildung und dementsprechendem Schadstoffausstoß.
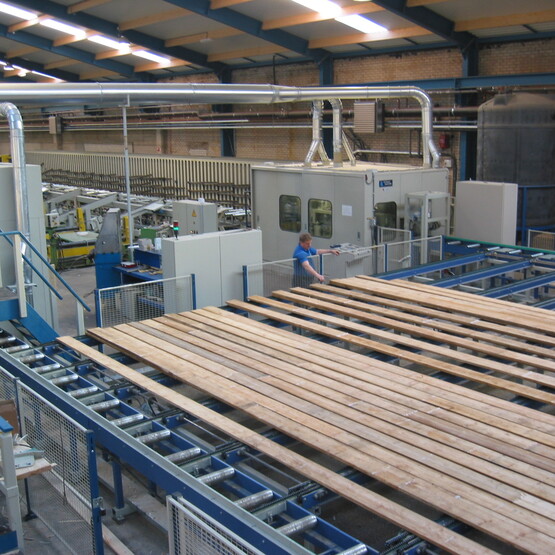
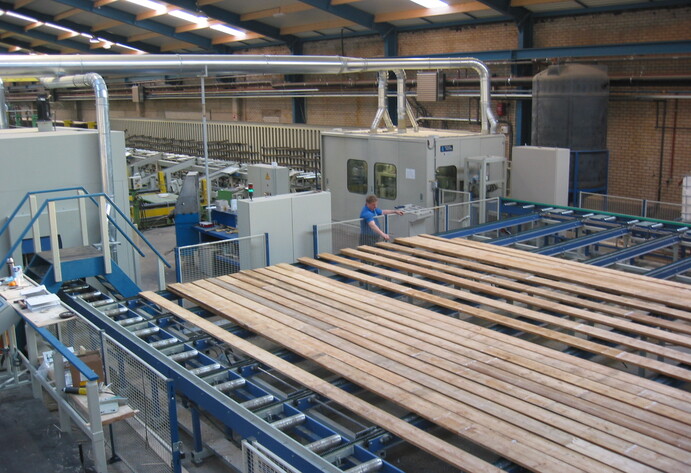
Holz im Schichtbetrieb: das Brettschichtwerk
Neben massiven Brettern, Profilhölzern oder auch Hackschnitzeln und Pellets sind Brettschichthölzer ein typisches Sägewerkprodukt. Hierfür werden mehrere Holzschichten mit Leim verbunden. Im kleinen Maßstab werden diese Stücke für den Möbelbau verwendet, da sie bis zu 36 Meter lang sein können, eignen sie sich aber ebenfalls hervorragend für den Bau von Holzhäusern.